How to solve the staining problem of 5052 aluminum plate? Today, aluminum panels are increasingly used in construction. Aluminum panels used in buildings include single-layer aluminum panels, composite aluminum panels and other materials. Among them, 5052 aluminum plate is widely used. The processing of 5052 aluminum plate has high requirements on cutting tools. Advanced aluminum plate processing tools can improve the mechanical properties of the aluminum plate and reduce unnecessary aluminum chips and sticking tools. However, dyeing problems may occur during the processing of 5052 aluminum plates. So, how to solve the dyeing problem of 5052 aluminum plates?
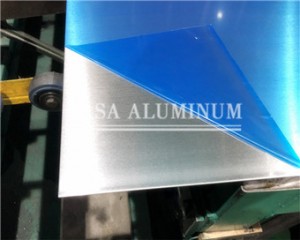
1. Control the thickness of the oxide film
Oxide film refers to the thickness, porosity, transparency, etc. of the aluminum plate film layer. The thickness of the film layer in the 5052 aluminum plate can be kept above 10um. The porosity and transparency can achieve good dyeing quality.
2. Choose good raw materials for 5052 aluminum plate parts
After the high-purity aluminum, aluminum-magnesium, and aluminum-manganese alloys in the production process are anodized, their dyeing properties are good and can be dyed into various colors. For plates with heavy silicon or copper content, they can only be dyed into dark and black, relatively monotonous colors during the dyeing process.
3. Master the concentration of the dyeing solution
There is a relationship between the concentration of 5052 aluminum plates and dyeing. If the aluminum plates are dyed light colors, the concentration can be lower, and if the aluminum plates are dyed dark colors, the concentration can be higher. The aluminum plate materials usually produced are dyed with a lighter color of 0.1-0.39g/L, a light color of 1g/L, a dark color of 3-5g/L, and a dense color of 10- 15g/L. If the dyeing concentration is high, it will cause uneven color or floating color, and "color bleeding" will easily occur during the cleaning and closing process. In order to enhance the adsorption of dyeing, low-concentration colors are used for extended dyeing, which allows the dye molecules to penetrate evenly into the depths of the pores of the oxide film, making the dyed color more harmonious and firm.
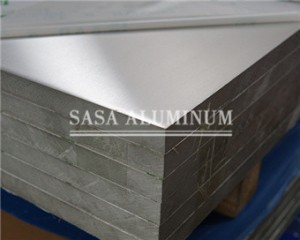
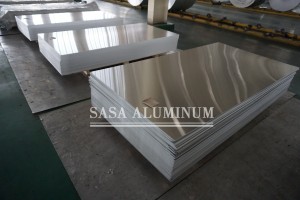
4. Control the temperature of the dyeing solution well
The dyeing of 5052 aluminum plates is divided into cold dyeing and hot dyeing. Using cold dyeing takes a longer time during the production process, and the uniformity of the dyed color is better controlled. Heat dyeing takes a shorter time, but it is more difficult to control the color. The temperature of heat dyeing is usually 40-60℃. If the temperature is too high, it will reduce the adsorption of dyeing and easily cause the surface of the aluminum plate to bloom.
The above is about how to solve the dyeing problem of 5052 aluminum plate. The use of 5052 aluminum plate is mainly used for low-load parts that require high plasticity and good weldability and work in liquid or gas media, such as mailboxes, gasoline or lubricating oil. Conduits, various liquid containers and other small load parts made by deep drawing: wire is used to make rivets. It is also commonly used in sheet metal parts of transportation vehicles and ships, instruments, street lamp brackets and rivets, hardware products, electrical appliance casings, etc.
Post time: May-14-2024